TUFS
THERMAL
UNDER FLOOR SYSTEM
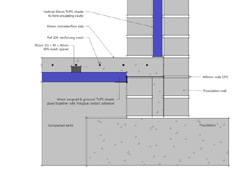 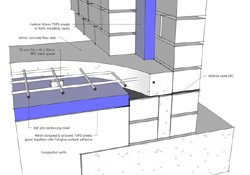
INTRODUCTION
Thermal insulation of buildings is becoming increasingly
relevant
as energy costs rise and climate change a reality.
Expanded polystyrene (EPS) is one of the most efficient
and cost effective materials
to provide thermal insulation in buildings.
One area that acts as a thermal heat soak is the under
floor area of any building drawing heat generated
inside buildings into the ground.
The TUFS under floor insulating system acts as a easy
to install under floor insulation system as well as
having a number of other functions and benefits.
PRODUCT DESCRIPTION
• TUFS is a 40mm thick, EPS, under floor, thermal
insulating system used as an integral part of ground
floor slab systems between conventional foundation
walls.
• TUFS panels are 1,2 x 1,2 m square and are
joined together by tongue and groove edging and a
propriety expanded polystyrene adhesive.
• TUFS prime function is to insulate ground
floor concrete slabs but it also acts as a moisture
proof barrier replacing the continuous plastic sheeting
normally used for this purpose.
• The TUFS sheets substitute approximately 50%
of the concrete used in conventional concrete floors
and due to the lower concrete volume the steel mesh
size used can also be reduced.
• TUFS can also be used as an EPS thermal insulating
cavity former in external brick walls. In this application
it will also have a dual function of creating an ‘in
wall’ moisture barrier.
PRODUCT
BENEFITS
Ground
floor insulation
EPS is used in a multiplicity of applications for
its thermal insulating properties. TUFS acts as a
thermal barrier to prevent under floor cold penetrating
rooms and keeping heat generated in houses from being
dissipated into the ground.
As a vertical brick wall ‘cavity former’
TUFS will act as an in wall thermal insulation barrier.
Water proof barrier
EPS is impervious to water and with the combination
of the TUFS tongue and groove joining of the sheets
secured by a glue line provides a continuous under
floor moisture barrier. Plastic sheet DPC membranes
are thus no longer necessary.
If used for wall insulation TUFS will also work to
create a vertical moisture barrier.
Concrete reduction
and reduction of potential for surface cracking
The 40mm TUFS sheets replace almost half of the concrete
used in a conventional 85mm ground floor slab reducing
cement usage and the heavy labour required in placing
the concrete.
As the concrete volume is halved the shrinkage stress
of the concrete is reduced and as the EPS spacer blocks
ensure the reinforcing mesh sits just below the floor
surface its function to reduce cracking is
optimised.
Reinforcement
mesh size reduction
As the concrete volume is reduced the mesh size can
be reduced typically from a 193 mesh to a 100 mesh.
This reduces the cost and eases material handling.
Optimisation of
underfloor heating systems
If under floor heating is installed the TUFS system
should be obligatory. TUFS will ensure that heat generated
is not absorbed by the ground and is forced upwards
into the house itself.
Floor Loading
Typically design loadings for floors should be:
|
Domestic |
Non-Domestic |
Intensity
of distributed load (kPa) |
1,5 |
2,5 |
Concentrated
loads(kN |
1,4 |
2,7 |
TUFS flooring can support these loadings without undue
deflection.
Long life
EPS is rot and rodent proof and dimensionally stable
and thus will retain its thermal insulating and moisture
barrier effectiveness for the life of the building.
Cost
The elimination of the need for plastic sheet DPC,
the substitution of concrete with EPS at near cost
equivalence and the reduction of the size of the reinforcing
mesh means that the TUFS composite floor system will
give the advantages of thermal insulation at no extra
cost.
When used as a vertical thermal insulating cavity
TUFS will ass a nominal amount to the building cost
providing significant benefits reducing energy consumption
required for heating and cooling.
PRODUCT SPECIFICATION
EPS sheets:
Expanded polystyrene sheet size: 1,2 x 1,2 m x 40mm
thick
EPS density: 16 gm/lt
Fire retardant additive: YES
Edge configuration: 2 sides 10mm deep x 20mm thick
rectangular tongue
and 2 sides 10mm deep x 20mm high groove.
Thermal conductivity: 0,038 w/mK
EPS spacers:
Expanded polystyrene blocks: 35mm high x 40mm square
with 5mm cross groove on upper surface
Number: 4 per each standard TUFs sheet
Adhesive:
Polyglue SBR expanded polystyrene adhesive packed
in 1 and 5lt tins.
1lt of Polyglue will be sufficient to glue 20-25 TUFS
sheets.
Sales code:
TUFS001 = 1,2m X 1,2m x 40mm TUFS sheets
SYSTEM
APPLICATION
UNDER FLOOR:
1) Concrete strip foundations and foundation walls
are built as normal
2)
Stepping of external walls to accommodate the floor
slab is done as normal.
3) Compact earth up to the under side level of the
floor slab.
4) Strip plastic DPC is laid on top of the brick course
on which the floor slab will rest.
5) TUFS sheets are laid from the inner edge of the
brickwork over the compacted area starting from a
corner, glueing and locating the tongue and groove
sheets as the area is covered. TUFS sheets are cut
with a handsaw or knife to fit exactly into the walled
area and offcuts kept to use elsewhere and prevent
wastage.
6) The bottom of the TUFS sheets should be about 20mm
below the top surface of the inner brick to allow
a 65mm covering of concrete.
7) 35mm thick 40 x 40mm EPS steel mesh spacer blocks
are fitted to the underside of the steel mesh before
laying this onto the TUFS sheets. This ensures that
the steel mesh is located where it is most needed
to prevent shrinkage cracking of the concrete - just
below the top of the concrete surface. 4 spacer blocks
are used per TUFS sheet.
8) Electrical ducting etc can still be run in the
concrete top section but if larger piping is run in
the floor this can be cut into the EPS sheets.
9) Concrete is then poured to complete the composite
floor construction and surface finished as normal.
IN WALL:
1) Build one skin of brick wall place TUFS sheets
vertically against the bricks and then proceed to
build other brick skin wedging the TUFS sheets in
the centre.
2) Glue the tongue and groove sheets and cut to fit
around windows and doors.
3) Final wall thickness will be 260mm as opposed to
conventional 220mm.
|